§ 9. соединение деталей шкантами и шурупами в нагель
Содержание:
- Использование нагелей в строительстве домов и бань
- Формирование углов на ус
- Нарезка внешней и внутренней резьбы на дереве
- Торцевое соединение досок
- Мебельный кондуктор своими руками: чертежи с размерами в помощь
- Применение
- Последовательность монтажа
- Характеристики промышленного строительного оборудования
- Рифление боковых поверхностей
- Технология крепления
- Соединения со специальными связями
- Соединение «гнездо-шип»
- Шиповое соединение (шип-паз)
- Тщательно планируйте последовательность сборки
- соединение деталей
- Изготовление метчика для резьбы на дереве своими руками
- Основные породы древесины
Использование нагелей в строительстве домов и бань
Шканты деревянные применяют при возведении различных сооружений с бревенчатыми или брусовыми стенами. Их использование утверждено нормативами строительных организаций, проектами домов из дерева. На практике применение березовых шипов обеспечивает деревянным основаниям безупречное соединение. Оно отличается подвижностью вертикального уровня. Однако это не мешает древесине осуществлять естественную усадку.
Использование шкантов в изготовлении мебели берёт своё начало ещё с «советских» времён. Но, несмотря на свою «древность», данный тип мебельной фурнитуры иногда используется и современными мебельщиками. Истории известны также некоторые личности, которые и по сей день продолжают использовать шканты для соединения всех узлов мебели, несмотря на то, что они живут в век высоких технологий и развития китайского промышленного плагиата всех современнейших элементов фурнитуры, разработанных в Европе.
Причину такой «любви» к шкантам объяснить сложно. Дело в том, что установка шканта требует высокой точности от мастера. Ошибка даже на долю миллиметра может привести к смещению деталей, исправить которое без «жертв» практически невозможно. Приходится либо рассверливать отверстие (что ведёт к ненадёжному соединению деталей), либо ставить в просверленное отверстие заглушку и сверлить его заново (что отнимает массу времени и нервов).
В общем, рискнём предположить, что мастера, продолжающие работать со шкантами, либо мазохисты, либо работают в очень дешёвом рыночном сегменте (так как единственным достоинством шканта, является его низкая стоимость). А может, живут где-то высоко в горах и работают с «дедовскими» запасами ДСП и фурнитуры, поэтому просто не знают о существовании конфирматов, уголков, и даже минификсов. Несмотря на нашу «нелюбовь» к минификсам, шкант можно отнести к ещё более «жёсткому» типу фурнитуры в плане его установки и регулировки.
Всё же мы решили рассмотреть технологию сверления отверстий под шкант.
Формирование углов на ус
Одним из лучших способов создания углов различных объемных изделий является стык на ус. Он позволяет создать монолитную конструкцию, скрыть волокна торца, тем самым обеспечить привлекательный вид. Этот способ подходит для самых разнообразных изделий, но чаще всего применяется для изготовления рамок и деталей корпусной мебели.
Для создания соединения в каждой из деревянных деталей делают пропилы под углом, равным половине угла, под которым встречаются заготовки. Чаще всего этот угол прямой, следовательно, запилы выполняют под 45 градусов, тем не менее угол может варьироваться в широких пределах. Работы выполняют по следующему алгоритму.
Вначале размечают детали
Важно не забывать, что разметка выполняется по длинной стороне, в противном случае можно не угадать с размерами
На кромках, которые будут соединены, проводят линию под требуемым углом. Комбинированным угольником разметку переносят на каждую сторону заготовки. Затем выполняют распил, для которого лучше использовать электрическую торцовую пилу, но можно работать и ручным инструментом
Работая ножовкой, важно контролировать угол среза, нелишним будет воспользоваться бруском в качестве направляющей
Готовые детали прикладывают друг к другу, проверяя точность подгонки. Неровности придется сгладить ручным рубанком, довести угол с помощью шлифовальной шкурки. На обе поверхности наносится столярный клей, и с помощью струбцин изделие фиксируется. Дополнительной прочности можно добиться с помощью гвоздиков
Работая молотком, важно контролировать силу удара, чтобы заготовки не сдвинулись
Особо ответственные соединения усиливают с помощью брусков, которые вклеивают во внутренний угол. Стык, который не будет виден, можно дополнительно укрепить металлическим угольником.
В результате качественно выполненной работы получится идеальный шов. Если же образовалась небольшая щель, то ее можно скрыть, расправив прилегающие волокна древесины с помощью гладкой цилиндрической поверхности. Для этого подойдет стержень обычной отвертки.
Нарезка внешней и внутренней резьбы на дереве
Для того, чтобы нанести на дерево резьбу используются такие инструменты как метчик (резак) и плашка. С их помощью наносят, как внутреннюю, так и наружную резьбу. Но для того чтобы провести такие работы нужно:
- учесть плотность древесины, так как не каждая пригодна для таких процедур;
- внутренняя резьба требует предварительно просверлить отверстие, диаметр которого должен быть меньше диаметра метчика;
- после отверстие очищается от стружки;
- для более успешной работы стоит воспользоваться маслом, например, льняным, его следует совсем немного капнуть в отверстие, а затем уже вставлять метчик.
Угол, под которым вводится метчик должен быть прямым ни в коем случае нельзя допускать перекосы иначе деталь будет испорчена.
Что касается внешней резьбы, то она наносится примерно таким же способом:
- диаметр заготовки должен равняться диаметру плашки;
- после наносится масло.
Помимо плашки можно использовать и обычную гайку:
- смазанная маслом заготовка размещается в тиски;
- далее медленно при помощи ключа вкручивают гайку.
После того, как нужное количество желобков нарезано, так же аккуратно ее выкручивают.
Торцевое соединение досок
Есть еще одно определение такого соединения — наращивание. Оно характеризуется тем, что все детали скрепляются между собой в торцевой части, при этом увеличивается длина целой детали. В зависимости от типа крепления такие торцевые соединения могут выдержать большие нагрузки при сжатии, растяжении и изгибе. Обычная целая доска здесь во многом уступает доске, полученной при наращивании.
Торцевое соединение деталей, сопротивляющееся сжатию может иметь различную конструкцию. Основная особенность этого соединения состоит в том, что каждый брусок обладает и накладкой, и пазом, которые чаще всего делаются равными и по толщине и по длине. Вы можете сделать наращивание с прямой накладкой вполдерева, а можете сделать торцевое соединение с косой накладкой.
Наращивание, сопротивляющееся сжатию, с прямой накладкой вполдерева
Наращивание, сопротивляющееся сжатию, с косой накладкой
Если вы не уверены в прочности будущего соединения, то можете дополнительно усложнить его шипами или различным стыком. Естественно, это соединение требует дополнительного клеевого крепления или крепления при помощи гвоздей и шурупов.
Торцевое соединение деталей, сопротивляющееся растяжению в основе своей конструкции содержит накладку в замок. Прежде всего вам необходимо расчертить накладку. Затем на одной детали сделать паз, а на другой — выступ. Именно этот замок и позволит обеим половинам избежать разъединения.
Так же, как и соединение, сопротивляющееся сжатию, этот тип соединения может иметь прямую накладку и косую накладку.
Наращивание, сопротивляющееся растяжению, с прямой накладкой
Наращивание, сопротивляющееся растяжению, с косой накладкой
В качестве дополнительного крепления здесь можно использовать клей, гвозди или шурупы.
Торцевое соединение, препятствующее изгибу, в своей основе использует накладку либо с косым стыком, либо накладку со ступенчатым стыком.
Наращивание, сопротивляющееся изгибу, с косым стыком
Наращивание, сопротивляющееся изгибу, со ступенчатым стыком
Особенностью первого типа соединения, где используется косой стык, является то, что торцевые стороны обеих деталей срезаются под острым углом. При этом при выпиливании торцов вы должны с точностью до нанометра соблюдать угол среза.
Второй тип соединения характеризуется тем, что на торцевых сторонах деталей есть небольшие пазы и шипы.
Оба перечисленные типы соединений обязательно должны иметь прямую поверхность накладок. Накладки с косой поверхностью используются достаточно редко, хотя они не уступают по прочности прямым. Для дополнительного крепления здесь в одинаковой степени могут использоваться клей, шурупы или гвозди.
Дополнительное крепление больших брусьев, использующихся при строительстве домов, может быть металлическим или деревянным. В качестве деревянных креплений используются шипы как выдолбленные, так и вставные.
Металлические крепления могут быть в виде хомутов или обмотки толстой проволокой. Нередко встречается крепление болтами.
Мебельный кондуктор своими руками: чертежи с размерами в помощь
Принцип этой оснастки:
- Корпус углового типа. Накладывается на плоскости деталей, которые потом будут соединяться между собой.
- Втулки направляющие. Через них будет входить сверло.
- Зажимные устройства. Они фиксируют кондуктор и выполнены с торцевой части.
Проектирование собственного кондуктора должно основываться на том, чтобы с помощью этой оснастки можно было делать большую часть выполняемых работ, связанных с крепежами различных типов.
Важно! Коль нужен универсальный помощник — это касается профессиональных мебельщиков, то лучше будет приобрести промышленную оснастку, которая сделана более точно и качественно. Именно такое приспособление будет предпочтительным и быстро себя окупит, особенно, если ещё учесть и то, что к этому устройству зачастую прилагается немало различных шаблонов, упоров и других мелочей, которые также необходимы в работе
Обходятся они гораздо дешевле, чем при покупке в розницу.
И всё же это приспособление, по необходимости, можно сделать своими руками.
Такая оснастка, возможно, нужна не так уж и часто в том или ином производстве, а уж домашнему мастеру — тем более. Так что многим пользователям сделать её самому будет значительно выгоднее.
Если же проектирование таковой остаётся актуальным, то нужно подготовить материалы для изготовления самодельного кондуктора для сверления под конфирмат:
- Уголок. Свой выбор следует остановить на неравнополочном виде этого проката — его возможности более широки. Полку уголка надо выбирать наибольшей толщины, которая может доходить до 8 мм. Это вполне обосновано, поскольку тогда можно вставлять направляющие втулки, наружный диаметр которых достигает 6 мм. Исходя из этого, можно использовать свёрла от 3,5 до 4 мм. Если даже того диаметра и будет недостаточно, то материал рассверливают большим сверлом, не используя уже никаких других приспособлений.
- Направляющие втулки. Здесь будут предпочтительнее трубы из нержавеющей стали, которые подбираются, прежде всего, по внутреннему диаметру. Пример: труба 6×1,5 подходит для сверла не более 2,7 диаметром. Разъяснение: внутреннее отверстие её будет 3 мм, а небольшой зазор по всему внутреннему диаметру учитывается из-за термического расширения материала. Длина втулки — это глубина отверстия в уголке, умноженная на два и более. Посадка втулок либо переходная, либо с натягом, либо по системе вала. Последняя является наиболее целесообразной.
Читать также: Как мерить сечение кабеля
Вместо труб, конечно, можно использовать готовые втулки, применяемые в аппаратах по протяжке проволок — таковые имеются, например, в машиностроении. Такие детали (даже бывшие в употреблении), подойдут как нельзя кстати: они выполнены из легированных сталей и имеют практически неограниченный ресурс работы.
Выбор способа крепления
- Фиксация при помощи саморезов. Они вкручиваются в деталь, что не допускает смещения приспособления из-за силы трения. Это удобно тем, что эти отметки понадобятся для последующего сверления других отверстий.
- Упор пружинный. Он будет надёжно фиксировать кондуктор на детали. Для такого упора подойдёт плоская пружина с соответствующей силой прижима.
- Струбцины внешние. Под них необходимо подкладывать резиновые прокладки. В качестве материала идеально подойдёт рифлёная резина. Это, конечно, немного увеличивает вес оснастки, а эластичность подкладок может негативно повлиять на перпендикулярность втулок. Чтобы этого не произошло, сверло заводят во втулку с целью разметки отверстия, а уж потом зажимаются струбцины.
Применение
Данные изделия издавна применяются и обширно распространены в металлообработке. Так, кондукторами комплектуют многие станки. Нужда в шаблонах для шкантов в сфере деревообработки обусловлена распространенностью закрытых мебельных соединений. В данной отрасли промышленности рассматриваемые приспособления применяют как в серийном производстве, так и при сборке. В последнем случае мебельные кондукторы служат для сверления отверстий под шканты.
Помимо названных сфер, такие устройства востребованы в строительстве, машиностроении, бытовых работах.
Сфера применения определяется типом кондуктора. Так, накладные устройства служат для обработки плоских деталей, плит ДСП и МДФ. Угловые применимы как для мебели, так и для плит ДСП и МДФ. Поворотные изделия рассчитаны на проделывание отверстий в цилиндрических деталях. Универсальные модели подходят для мелкосерийного мебельного производства. Опрокидываемые варианты рассчитаны на одновременную обработку в нескольких плоскостях. Закрепляемые и скользящие кондукторы наиболее подходят для бытового использования. К тому же последние несовместимы с одношпинделевыми станками.
Жесткие модели ориентированы на проделывание отверстий в предметах с неровной плоскостью вроде труб. В рассматриваемом случае их закрепляют с применением струбцины, но для мебели названный способ не подходит, так как возможна деформация поверхности.
Использование кондукторов упрощает и ускоряет осуществление работ за счет того, что это избавляет от необходимости ручных замеров и расчетов.
Последовательность монтажа
Порядок работы с деревянными шипами сводится к следующим пунктам: вначале требуется найти середину на нужной плоскости и сделать разметку будущего отверстия.
- С помощью сверлильного станка необходимо сделать углубление. В него будет вставляться шип. Диаметр сверла должен быть таким же, что и у шканта. Глубина – 1,5 бруса.
- Если крепеж будет находиться в отверстии слишком свободно, то он не сможет выполнять свою функцию полноценно. В случае излишней плотности и выступания нагеля над поверхностью могут появиться проблемы в результате естественной усадки здания.
- При обработке отверстия нужно следить за тем, чтобы угол сверла был перпендикулярен основанию. Это поможет избежать проблем при соединении деталей. Нагель соединяет 2 бруса или бревна, причем делать это нужно с соблюдением шахматного порядка по периметру стены сруба. При этом допустимым расстоянием между ними будет 1000-1500 мм.
- От совмещения чаш и проемов необходимо делать отступ в 300 мм. При монтаже уровень влажности шкантов должен совпадать с влажностью самого бруса.
- В полученное отверстие необходимо вставить кнопки-керны, предназначенные для разметки отверстия на другой доске. При отсутствии такой детали вполне можно прибегнуть к самостоятельному изготовлению. Для этого нужно сделать заточку стержня в виде карандаша так, чтобы в середине была иголка. Вставить его в отверстие.
- Затем две доски укладываются на ровную поверхность, слегка прижимаются друг к другу. Таким образом, на чистой доске появляется разметка для высверливания углубления для шипа.
Нагель должен плотно и без скосов сидеть в пазах бруса, иначе он не выполнит свою функцию.
Для таких целей можно воспользоваться разметочным рейсмусом
Здесь важно правильно найти середину нужных поверхностей
В полученные отверстия нужно вставить стержень, части досок обработать клеем, соединить заготовки и зажать в струбцину. Затем необходимо высушить конструкцию.
Советы:
- Делать отверстия под шканты следует правильно. Это соединение имеет свою особенность: его нельзя изменять в момент сборки.
- Обязательным условием является просверливание углублений строго перпендикулярно.
- Не стоит делать чересчур глубокие дырки, это может привести к выходу нагеля за пределы доски. Торчать они не должны.
Характеристики промышленного строительного оборудования
С повышением мощности изменяются параметры рабочих поверхностей, например, размер шпинделей увеличился до 23 мм. Вторым отличием является степень удаления последнего шпинделя от остальных на расстояние 70,5 см. Данное технологическое решение позволяет использовать под шканты пневматический агрегат. Остальные технические характеристики выглядят таким образом:
- мощность электродвигателя — 1,9 кВт;
- параметры столешницы — 79х38 см;
- отличается глубоким сверлением до 9 см.
Перечисленные характеристики не являются истиной в последней инстанции. В зависимости от характера выполняемой работы подбирается определенный агрегат. Делается это с учетом двух факторов. Первый — порода используемой древесины. Чем она прочнее, тем большая глубина сверления понадобится. Запас должен быть не меньше 1,5 см. Этого будет достаточно для обеспечения высокого качества работы.
Второй фактор — возможность быстрого перехода между режимами работы. Данная опция в равной степени актуальна для промышленных производств и небольших мастерских. К примеру, требуется выполнить обрезку заготовки под углом 45,5°. В этом случае на помощь придет усозарезной станок. Благодаря возможности быстрого регулирования угла наклона лезвия, даже оператор-новичок справится с поставленной задачей.
Правильно изготовленный шкант обеспечит надежное крепление 2 деталей. В их производстве используются различные станки. Глубина сверления, угол наклона лезвия, максимально допустимая длина и диаметр обрабатываемой заготовки — все это учитывается до момента покупки и установки оборудования. Не стоит упускать из поля зрения мощность электродвигателя.
Чем активнее планируется использовать агрегат, тем выше данный показатель должен быть. В противном случае велик риск вывести из строя «сердце» станка. Рекомендуется также подумать о системе предохранителей. Она снизит вредоносный эффект резкого скачка напряжения и убережет инструмент от поломки, которая, в свою очередь, может не подлежать ремонту.
Рифление боковых поверхностей
Рифление боковых поверхностей шкантóв Деревянные шканты могут иметь на боковой поверхности продольные пазы — рифли, как прямые, расположенные вдоль (параллельно) оси цилиндра, так и винтообразные. Некоторые виды пластмассовых шкантов имеют на боковых поверхностях «заершённость». Рифли служат для выхода воздуха при установке шкантов в деталь, а также для прохода и лучшего сцепления клея при соединении «на шкант». «Заершённость» шканта предотвращает выпадание из удерживающей его детали при необходимости обеспечения разборности соединения.
Виды рифления боковых поверхностей шкантов (на фотографии сверху вниз):
- Прямые рифли — рифление для шкантов универсального назначения;
- Винтообразные рифли — рифление для шкантов, предназначенных для клеевого соединения;
- Сложные рифли — (в данном случае винтовые и поперечные рифли) рифление для шкантов, предназначенных для усиленного клеевого соединения;
- Поперечные рифли — дополнительное рифление для шкантов, предназначенных для усиленного клеевого соединения.
Также возможно изготовление шкантов без рифлей, то есть с гладкой боковой поверхностью.
Технология крепления
Чтобы построить качественный уютный дом, который простоит не одно десятилетие, нужно строго следовать правилам строительства.
Как расположить деревянный нагель
Прежде всего, нужно рассчитать, сколько нагелей потребуется поставить для бруса определенной ширины. Определить их месторасположение, расстояние между ними. Исходя из этого, сделать нужное количество крепежных элементов. Лучше выполнить подготовительную работу, чтобы в процессе монтажа не отвлекаться, если крепежа вдруг не хватит.
Каждый нагель скрепляет между собой два бруса. Специалисты рекомендуют следовать следующим советам:
- Чтобы отметить первое отверстие, от края бруса отступают 300-700 мм.
- В зависимости от диаметра нагеля, шаг отмеряют 1,5 – 2 м.
- Элементы лучше располагать в шахматном порядке.
Сверление
Сверлить отверстия нужно ровно по центру бруса. Положение работника должно быть устойчивым, чтобы оно получилось строго вертикальным. Диаметр выбирают равным толщине крепежа, чтобы впоследствии тот можно было забить киянкой. Это помогает избежать провисания конструкции из-за небольшой вертикальной нагрузки.
Глубина определяется как длина штыря плюс 2-3 см. Это компенсирует нагрузку при усадке стены. Дрель для сверления бруса под нагели выбирают мощностью не менее полутора киловатт с большим набором сверл.
Забивание
Нагеля должны входить в отверстия легко, с небольшим натягом. Если приходится прикладывать силу для забивания, вместо того, чтобы снимать напряжение, деталь его добавит. Древесина может потрескаться еще на этапе строительства.
Хорошо снижает трение при забивании мыльный раствор.
На забитые в отверстия крепления надевается следующий венец.
Иногда во время строительства по разным причинам приходится принимать неординарные решения. Это обогащает опыт начинающего мастера.
Соединения со специальными связями
Практически все столярные соединения выполняются с дополнительными укрепляющими связями. В самом простом примере роль таких выполняют гвозди или саморезы.
При наращивании деталей узел может укрепляться сквозным болтовым соединением, хомутами, скобами и глухарями, либо его просто обматывают холоднокатаной проволокой. Сращенные вертикальные опоры достаточно скрепить двумя накладными планками — деревянными или металлическими.
Угловые соединения чаще всего скрепляют скобами, накладными пластинами или уголками. В случаях, когда надо сохранить небольшую подвижность соединения, используют один сквозной болт, который либо прошивает поперек место накладки деталей, либо стягивает их в продольном направлении с минимальным отступом от накладки.
Место крепления специальной связи должно быть удалено от края не менее чем на 10 диаметров крепежного элемента и не иметь пороков
Важно помнить, что часто связи не обеспечивают общую прочность соединения, а только компенсируют неучтенную нагрузку
Соединение «гнездо-шип»
Наиболее часто используемый способ соединения деревянных деталей. Такое сочленение прочное, жесткое и выглядит максимально аккуратно. Чтобы выполнить такое соединение, нужно иметь некие навыки и опыт, а также быть внимательным. Неправильно выполненное соединение «гнездо-шип» непрочное и выглядит некрасиво.
Суть его следующая. В конце одной заготовки высверливается или выдалбливается паз, а в конце другой — шип. Лучше, когда элементы имеют одинаковую ширину. Если толщина разная, то шип проделывают в тонкой детали, а паз, соответственно, в толстой.
Последовательность шипового соединения:
- Используя рейсмус, прочертить две параллельные друг другу риски сбоку одной заготовки. Расстояние должно быть по ширине будущего шипа. Для его ровности следует сделать разметку с двух сторон.
- Наиболее оптимальный инструмент для выполнения шипов — ножовка, имеющая узкое полотно и мелкие зубья, или лучковая пила. В процессе работы зубья инструмента должны проходить по внутренней кромке разметочной линии. Для удобства деталь лучше зажать в тисках. Лучше всего шип изготовить чуть больше требуемого размера. Тогда в случае необходимости можно убрать лишнее. А вот если шип окажется короче, то весь процесс потребуется повторить заново.
- Используя долото или стамеску, во второй детали делают гнездо (паз). Естественно, размеры паза должны соответствовать размерам шипа. Лучше всего перед тем, как приступить к долблению, по всему периметру паза просверлить отверстия. Края аккуратно обрабатываются стамеской.
Если соединение деревянных деталей выполнено правильно, то поверхности кромок шипов прилегают плотно к стенкам гнезда. Это дает хорошее сцепление при склеивании. Чтобы посадка шипов была более тугой, их размеры должны быть на 0,2-0,3 мм больше размеров гнезда. При превышении этой величины может произойти раскол тетивы, при допуске меньше крепление потеряет свою прочность в процессе эксплуатации.
Кроме того, такое соединение предполагает еще склеивание и крепление шурупами, гвоздями или деревянными нагелями. Для упрощения работы перед ввинчиванием шурупов следует просверлить отверстия. Головки шурупов скрывают в потай (выполненный с помощью зенковки). Направляющее отверстие должно быть равно 2/3 диаметра винта и быть меньше на 6 мм (приблизительно) его длины.
Шиповое соединение (шип-паз)
Самым простым и одним из самых надежных является соединение шип-паз. Оно широко применяется в столярном деле. Подобным способом собирают в единое целое деревянные детали оконных рам, изготавливают самые различные детали корпусной мебели, листы фанеры. Суть данного способа состоит в том, что на торце одной соединяемой детали делают шип, который вставляется в паз другой детали и фиксируется в нем.
Для работы удобно использовать специальный ламельный фрезер, за неимением такового можно обойтись простым ручным инструментом. Понадобится:
- ручная обушковая пила с мелким зубом;
- электрическая или ручная дрель;
- несколько стамесок разной ширины;
- наждачная бумага;
- измерительный инструмент, угольник и карандаш.
Сначала размечают заготовки. Параметры шипа и паза зависят от параметров деревянных деталей и конфигурации изделия, тем не менее стоит учитывать несколько общих рекомендаций.
Параметры паза также должны соответствовать этим критериям
В любом случае важно следить за тем, чтобы размеры шипа и паза совпадали. Детали должны соединяться легко, без нажима, но не выпадать под собственным весом
Не должно быть люфтов, щелей и перекоса.
Первым вырезают паз, такая последовательность вызвана тем, что шип гораздо проще подгонять под паз, чем наоборот. С помощью пилы делают пропилы, лишнюю древесину удаляют с помощью дрели, дно паза и стенки выравнивают стамесками.
Далее делают шип. Брусок зажимают в тиски и ручной ножовкой удаляют лишнюю древесину. До требуемых размеров шип доводят с помощью стамесок и шлифовальной шкурки.
В большинстве случаев для фиксации деталей достаточно одного лишь столярного клея, обеспечить максимум прочности помогут шурупы или гвозди.
Тщательно планируйте последовательность сборки
Вы аккуратно выпилили все детали, добились плотности во всех соединениях и теперь готовы заняться сборкой. Но прежде чем открыть флакон с клеем, обязательно проведите пробную сухую сборку (без клея). Собирая изделие, определите, в каком порядке лучше соединять детали, сколько струбцин потребуется для плотного сжатия всех соединений и как лучше разместить струбцины, чтобы не было перекосов.
Сборку больших и сложных проектов лучше разделить на несколько простых этапов, вместо того чтобы суетиться, пытаясь склеить все детали за один раз. Например, делая шкафчик с филенчатыми боковинами, сначала соберите рамы с филенками, а затем приступайте к основной сборке. Такой подход дает вам больше времени для проверки всех соединений и требует меньше струбцин. Другой способ выиграть время — использовать клей с увеличенным временем схватывания. Например, обычный желтый клей Titebond заставляет провести всю сборку за 15 минут, а разновидность Titebond Extend позволяет выравнивать склейку в течение 25 минут.
При установке струбцин убедитесь, что их давление приходится на середину соединения. Неправильно установленная струбцина может деформировать детали так, что между ними образуется зазор. Иногда, несмотря на все старания, соединения не получаются аккуратными. Случайно соскользнувший инструмент, невнимательность или незамеченные опилки около упора приводят к тому, что соединение оказывается неплотным или в нем появляется заметный зазор.
Собирайте шкафчик поэтапно, склеив сначала небольшие боковые филенчатые рамы. Тогда вы сможете уделить больше внимания каждому соединению. Затем приступайте к сборке корпуса
соединение деталей
Как и все простое, эти идеи, как изобретение велосипеда, приходят самостоятельно к мастерам-практикам.
На фотографии угол универсального столика до покраски.
Простое эстетичное соединение деталей на шкант (сквозное соединение).
К этому методу можно прийти двумя путями:
— стремясь уйти от шляпок шурупов или конфирматов в своих соединениях;
— стремясь технологично соединить детали на шкант
Первый путь вроде понятен: шляпки маячат… весь вид портят… а что если их выкрутить и вклеить шканты?
Второй менее очевиден: просверлил отверстия под шканты, проклеил места соединения, соединил детали, начал забивать шканты… все разваливается, между деталями образуется огромная щель… а может сначала склеить на шурупах?
Так правильно:
— собираем детали на минимуме шурупов;
— разбираем и проклеиваем детали;
— собираем уже с клеем и ждем пока высохнет;
— высверливаем дополнительные отверстия под шканты если нужно;
— забиваем в них на клей шканты чтобы края торчали;
— выкручиваем шурупы;
— аккуратно рассверливаем отверстия под шканты и повторяем 5 пункт;
— ждем пока высохнет;
— спиливаем торчащие концы шкантов;
— шлифуем.
Рассверливать уже существующее отверстие всегда надо аккуратно, потому что может разворотить край отверстия. Чтобы уменьшить вероятность возникновения данной проблемы можно:
— наклеить на отверстие малярный скотч;
— сначала сверлить против часовой стрелки.
Глухое соединение на шкант используется тогда, когда не хотят видеть следов такого соединения. Технология немного сложнее, так как обеспечить точную разметку и сверление отверстий для шкантов более проблематично.
Обеспечить точность можно несколькими способами:
- незамысловатый, с порчей гвоздей:
- забиваются маленькие гвозди в центры будущих отверстий для шкантов на одной детали;
- откусываются шляпки;
- подготовленная деталь совмещается с другой, и они сжимаются (в местах контакта с гвоздями образуются отметки);
- гвозди вынимаются;
- сверлятся отверстия по отметкам от гвоздей
- использование эталонных шкантов:
- делаем необходимое количество эталонных шкантов;
- высверливаем в обычных шкантах по центру отверстие и вставляем гвоздь (можно использовать карандаш, в нем уже есть по центру отверстие)
- обрезаем такой шкант так, чтобы при нормальной глубине оставалось только острие гвоздя и уменьшаем диаметр шканта, чтобы его можно было потом свободно вытащить из отверстия
- сверлим в первой детали отверстия под шканты (обычно это торец детали);
- вставляем эталонные шканты;
- совмещаем детали и делаем дальше все как и в незамысловатом способе.
- делаем необходимое количество эталонных шкантов;
- использование покупных маркеров.
- использование фирменных шаблонов для такого вида соединения.
Для второго способа надо соблюдать эталонную глубину сверления для первой детали.
Маркер для разметки под шканты выглядит так:
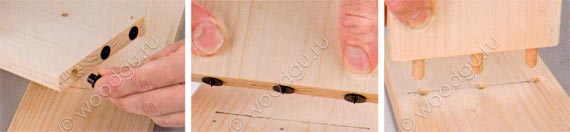
Видел в Леруа 8мм 4 шт. — 59 руб. (были маркеры и для других диаметров шкантов)
Клеевые соединения
Полезные советы:
- Клей лучше распределять по детали зубчатым шпателем, это обеспечит равномерный клеевой слой и как следствие прочное клеевое соединение.
- Также при планировании клеевых соединений, требующих повышенной прочности надо обеспечивать наибольшую возможную площадь такого соединения. Например, как в верхнем рисунке – горизонтальная деталь приклеена и снизу и с торца к своеобразной ступеньке вертикальной детали.
- Перед тем как склеивать детали, можно проклеить малярной лентой места, где может выступить клей.
Фиксация деталей при склейке.
Есть много способов фиксации:
— груз;
— струбцины и зажимы;
— клинья и распорки;
— куски малярного скотча;
— скретч пленка;
— веревки и стяжные ремни (рэтчеты);
— шурупы и гвозди;
— скобы строительного степлера (если одна из склеиваемых деталей менее 11 мм толщины)
— …
Временная фиксация скобами особенно удобна на больших площадях (фиксировать лучше из центра). Но есть несколько недостатков:
— при использовании перекаленных скоб часть скоб вытащить не удастся;
— после вытаскивания остаются маленькие дырочки (частично или полностью их можно закрыть, капнув в них воду).
В последнее время часто пользуюсь следующим соединением:
Как делается видно на фото. Фреза или сверло Форстнера на 35 мм + стандартный конфирмат.
сверление
>>>слeдующая>>> массив vs фанера |
струбцины и другие средства фиксации деталей обзор имеющихся у меня струбцин и ретчетов (стяжных ремней)… виды, достоинства, недостатки… советы какие лучше выбирать |
явайское соединение на шуруп (табуретка от PeLiDesign) простое и оригинальное открытое соединение или сращивание деталей на шурупах, которые потом декорируются резьбой |
Изготовление метчика для резьбы на дереве своими руками
Для нарезания резьбы в дереве, может потребоваться метчик по дереву, данный инструмент скорее всего обойдется не дешево, да и найти его может быть довольно сложно. Но не стоит расстраиваться, ведь подобную деталь, довольно легко изготовить самостоятельно. Для этого потребуется:
- угловая машина для шлифования;
- станок для заточки;
- дрель;
- далее необходимо подобрать болт или шуруп, на котором будет нужная резьба.
При использовании болта, сначала отрезают шестигранную головку, после заточным станком делают небольшую часть для захода, делают это путем вращения руками или закрепив конец в дрели. Далее, потребуется выточить канавки, в количестве 3-4 штук и очистить резьбу от попавшего вовремя вытачивания мусора, это можно сделать гайкой.
Основные породы древесины
Вся древесина разделяется на две большие группы: на древесину из хвойных пород и на древесину из лиственных пород дерева.
Хвойная древесина отличается высокой прочностью и устойчивостью к гниению. Древесина подобного типа обладает относительно небольшим весом.
Чаще всего в стране используют древесину сосны. Применяют ее для производства столбов, пиломатериалов, шпона, фанеры, для выработки целлюлозы, бумаги.
Древесина кедра обладает теми же свойствами, что и сосна, но используют кедр преимущественно для производства мебели.
Древесина ели используется реже всего — в основном для изготовления музыкальных инструментов. Пихта идет на изготовление дощечек для кровли. Древесина лиственницы содержит большое количество смолистых веществ, из-за чего плохо поддается гниению, в т.ч. при помещении ее в землю.
Для изготовления нагелей чаще всего используют древесину лиственных пород:
- акации;
- березы;
- дуба;
- ореха.
И только если нет выбора, разрешено использовать лиственницу и сосну. Если дом строится из древесины лиственницы, предпочтение отдают и нагелям, изготовленным из этого дерева. Ель для изготовления штырей не подходит. Лучшим деревом для изготовления нагелей считается береза. Для соснового бруса берут нагели из акации или дуба.
Соединение деталей шкантами и шурупами в нагель L-120 означает, что при сборке используют нагели, длиной 120 мм. Соответственно, надпись соединение шкантами и шурупами в нагель L-150 означает, что детали соединяются с использованием нагеля, длинной 150 мм. Значение, идущее за нагелем, означает длину штыря, о котором идет речь.
Древесина акации
Древесина березы
Древесина дуба
Древесина грецкого ореха